Food
Everything You Need to Know About Pelletierung
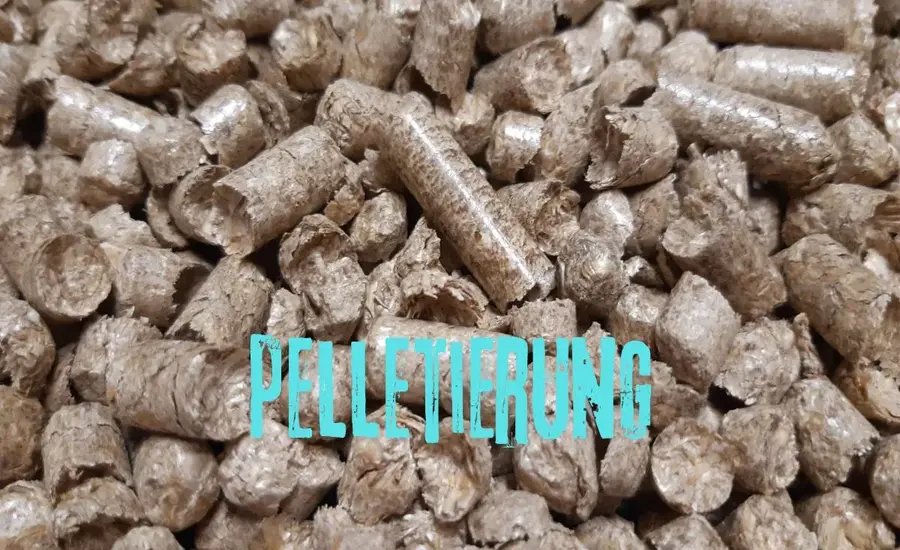
Pelletierung, or pelletizing, is a critical process in the manufacturing industry, used in a variety of applications, including pharmaceuticals, agriculture, food production, and especially in the production of high-quality fuel and animal feed. As industries around the world look for ways to improve efficiency, reduce waste, and create more sustainable products, pelletization has gained increasing significance. This comprehensive article will explore the entire pelletizing process, its benefits, applications, technologies involved, and the future of pelletization.
Understanding Pelletierung
At its core, pelletization is the process of forming materials into pellets — small, spherical or cylindrical shapes that have a high density and uniform size. The material can vary from biomass, metals, minerals, polymers, and more, depending on the specific industry. The process of pelletierung typically involves the use of heat, moisture, and pressure to agglomerate fine particles into larger, solidified forms. In the context of biomass, this process is used to create fuel pellets, which are used for heating and energy generation.
Historically, pelletization was an essential part of the mining industry, where raw ores and metals would be processed into pellets for easier handling and transportation. Today, it is most commonly associated with the production of fuel pellets, animal feed, and food products, though it has applications in numerous other sectors. The growing demand for environmentally friendly and sustainable alternatives to coal and other fossil fuels has particularly spurred the rise of wood pellets, made from sawdust, wood chips, and other plant matter.
The Pelletization Process
Pelletization involves several steps, each crucial to achieving the final product. From raw material preparation to the compression and cooling stages, every phase is designed to ensure that the pellets have the desired characteristics such as durability, size, and density.
- Material Preparation: Before the material is pelletized, it must be finely ground. This helps reduce the particle size, making it easier to form uniform pellets. Depending on the material, it may also need to be dried to a specific moisture content to ensure optimal pellet formation. For example, in the case of wood, the sawdust or wood chips must typically be dried to a moisture content of 10-15% for efficient pellet production.
- Mixing and Conditioning: After grinding and drying, the material is often mixed with additives, such as binders, lubricants, or other ingredients, to enhance the quality of the final pellet. For biomass pellets, binders can be added to improve the mechanical strength of the pellet and reduce the likelihood of breakage during handling. In some cases, steam may also be injected into the mixture to condition the raw material, increasing its plasticity and improving the flow during compression.
- Pelletizing: Pelletization itself is carried out using specialized machinery, often referred to as pellet mills or pellet presses. These machines compress the conditioned material between rollers or through a die. As the material passes through the die, it is forced into the shape of small, uniform pellets. Pellet mills can operate at varying levels of pressure, depending on the material being processed, and the temperature may rise due to the friction involved in the compression process.
- Cooling: After pelletizing, the pellets are hot and must be cooled to ensure they retain their shape and hardness. The cooling process also helps to reduce moisture content, which is essential for preventing mold growth and ensuring the pellets can be stored for long periods. Cooling is typically done using air or water systems that absorb the heat from the freshly formed pellets.
- Sifting and Packaging: Once the pellets have cooled, they are often screened to remove any fines or broken pellets. These fines can be recycled and reintroduced into the pelletizing process. The final pellets are then packaged for shipment, either in bulk or in bags, depending on the application and the market demand.
Pelletization Technologies
While the process of pelletization is fairly straightforward, the technologies used to execute it have evolved considerably over the years. Modern pellet mills utilize advanced techniques that allow for higher precision and efficiency.
- Ring Die Pellet Mills: Ring die pellet mills are among the most commonly used types of pellet mills in the industry. They are characterized by a vertical or horizontal cylindrical die that has multiple holes through which material is forced. The material is compressed into a small space, causing it to extrude into pellet shapes. Ring die pellet mills are generally favored for their higher output and efficiency, making them ideal for large-scale production operations.
- Flat Die Pellet Mills: Flat die pellet mills are another common design used in smaller-scale operations or for producing specific types of pellets. These mills have a flat die with holes through which the material is pressed. Flat die mills are often easier to maintain and are typically more cost-effective for lower-output applications, such as small farms or home heating systems.
- Auger Pelletizers: Auger pelletizers use a helical screw (auger) to move material through the pelletizing process. This technology is particularly useful when dealing with materials that need to be pressed at a lower pressure or when processing sticky or moisture-sensitive materials. Auger pelletizers are most commonly used in the food and pharmaceutical industries, where exact specifications of pellet size and density are important.
- Pellet Cooler Technology: Pellet cooling technology has advanced in recent years, with more sophisticated systems that optimize airflow and reduce cooling time. The ability to cool pellets quickly without cracking or compromising their quality is essential for large-scale production. Technologies such as counterflow coolers and fluidized bed coolers are commonly used to ensure that the pellets maintain their shape and durability.
Applications of Pelletierung
Pelletization has found a wide array of applications across numerous industries. Below are some of the most prominent areas where pelletizing plays a vital role.
- Biomass Fuel Production: One of the most significant uses of pelletizing is in the production of biomass fuel pellets, especially wood pellets. These pellets are used as an alternative to coal in power plants, industrial boilers, and residential heating systems. Wood pellets are renewable, produce lower carbon emissions than fossil fuels, and provide a sustainable source of energy. As concerns about climate change and environmental sustainability continue to grow, the demand for biomass pellets has surged in recent years.
- Animal Feed Production: Pelletized animal feed has become the standard in the livestock industry due to its convenience and efficiency. Pelletized feed is easier to handle, store, and transport than loose feed, and the uniform size and consistency of the pellets ensure that animals receive the right amount of nutrients. Pelletizing also helps to improve the digestibility of certain types of feed, particularly for poultry and aquaculture.
- Pharmaceuticals and Food Processing: Pelletization is also widely used in the pharmaceutical and food industries, where it is employed to create controlled-release medication, as well as for the production of uniform food products like breakfast cereals or snacks. In pharmaceuticals, pellets are often used as a way to ensure that active ingredients are released slowly over time, providing patients with consistent dosing throughout the day.
- Agricultural Fertilizers: The agricultural sector also benefits from pelletization, with fertilizers being one of the most commonly pelletized products. Fertilizer pellets are easier to distribute and apply evenly, ensuring that crops receive the correct amount of nutrients. This method of fertilizer application helps to minimize waste and reduce the impact on the environment, as excess nutrients can be minimized.
- Recycling and Waste Management: In the recycling industry, pelletization can be used to process waste materials, such as plastics and metals, into more manageable forms. By pelletizing materials, they can be more easily transported and processed into new products. Pelletizing is also increasingly used to process organic waste, converting it into biomass pellets for energy generation.
Benefits of Pelletierung
Pelletization offers numerous advantages, especially in terms of efficiency, sustainability, and handling. Some of the key benefits of pelletizing include:
- Enhanced Handling and Storage: Pellets are easier to handle, store, and transport than loose material, which makes them ideal for large-scale operations. Their uniform size allows for better packing and reduces the need for excessive space during storage.
- Improved Energy Density: Pellets have a higher energy density compared to their raw materials, making them more efficient as a fuel source. This higher density also means that more pellets can be transported at once, reducing shipping costs.
- Sustainability: Pelletizing helps reduce waste by making use of materials that would otherwise be discarded, such as sawdust, agricultural residues, and waste from manufacturing processes. Biomass pellets, in particular, are a renewable energy source that contributes to the reduction of greenhouse gas emissions.
- Consistency and Quality Control: Pelletizing allows for precise control over the size, density, and moisture content of the final product. This ensures that the pellets meet specific requirements for various applications, such as fuel efficiency or digestibility in animal feed.
The Future of Pelletierung
The future of pelletization is closely tied to the ongoing efforts to develop more sustainable, efficient, and cost-effective processes. As demand for renewable energy grows, the pellet industry will continue to evolve, with advancements in pellet production technologies aimed at increasing throughput, reducing energy consumption, and improving the quality of the pellets.
- Advanced Materials: Researchers are exploring new materials for pelletizing, including alternative biomass sources such as algae, municipal waste, and agricultural by-products. The focus is on expanding the range of feedstocks that can be used in pelletization without compromising efficiency or quality.
- Automation and AI: Automation and artificial intelligence (AI) are likely to play an increasingly important role in pellet production. AI-driven systems can monitor production conditions in real-time, ensuring optimal conditions for pelletizing. This can lead to more consistent production, reduced waste, and lower operating costs.
- Decentralized Production: The trend toward decentralized production, where small-scale pellet plants are located closer to the raw material sources, is expected to grow. This model reduces transportation costs and makes pellet production more accessible to regions that were previously underserved.
- Circular Economy: Pelletization will continue to play a key role in the circular economy, especially in waste-to-energy initiatives. Recycling waste products into usable pellets can help reduce landfill waste and create sustainable energy sources, contributing to the broader goals of sustainability and waste reduction.
Conclusion
Pelletierung is a vital process that has far-reaching applications across various industries. Whether it’s producing biomass pellets for energy, animal feed for livestock, or high-quality fertilizers for agriculture, the benefits of pelletization are undeniable. As technology continues to advance and sustainability becomes even more crucial, pelletization will remain at the forefront of efforts to create efficient, renewable, and environmentally friendly solutions for industries worldwide. With innovations in materials, production processes, and automation, the future of pelletization looks brighter than ever.
FAQs:
What is Pelletierung (Pelletizing)?
Pelletierung, or pelletizing, is the process of forming materials into small, uniform pellets using heat, pressure, and moisture. It is commonly used in various industries, including biomass fuel production, animal feed manufacturing, and even pharmaceuticals, to produce compact, easily manageable, and transportable pellets.
What materials can be pelletized?
Pelletization can be applied to a wide range of materials, including organic substances like biomass (wood, sawdust, straw), animal feed, and agricultural waste. It is also used for inorganic materials, such as metals, minerals, and plastics, in industries like mining, recycling, and manufacturing.
Why are pellets preferred over loose materials?
Pellets offer numerous benefits over loose materials, including better handling, storage, and transportation. Their uniform size and high density make them more efficient to store and ship, reducing costs. Additionally, pellets are less prone to spoilage or degradation, making them ideal for long-term storage.
What is the difference between a ring die and a flat die pellet mill?
Ring die pellet mills feature a cylindrical die with multiple holes and are typically used for large-scale operations due to their high output and efficiency.
Flat die pellet mills use a flat die with fewer holes and are better suited for smaller-scale operations or niche applications. They are often simpler to maintain and more cost-effective for lower-output production.
What is the ideal moisture content for pelletizing?
The ideal moisture content varies depending on the material being processed. For example, wood sawdust typically requires a moisture content between 10-15% for efficient pellet production. Too much moisture can cause issues with pellet quality, while too little moisture can make the material too dry to compress effectively.
-
Blog8 months ago
Discover The World Of Movies With Mkvcinemas.com
-
Biography9 months ago
Madeline Argy: Age, Height, and Family Background Revealed
-
Tech9 months ago
SimpCityForum: One of the Most Interesting Online Communities
-
Biography9 months ago
CelebrityMeet Christina Erika Carandini Lee?: All You Need To Know
-
Biography8 months ago
Mary Marquardt: The Woman Behind Harrison Ford’s Rise
-
Biography9 months ago
How Old Is SZA Daughter? Discover SZA Daughter’s Age, Name, and More
-
Crypto Currency9 months ago
5starsstocks .com: How It’s Useful and Helpful
-
Blog9 months ago
What is FilthyGrid? Exploring the World of FilthyGrid
-
Health & Fitness9 months ago
What Has Kiolopobgofit in It? Exploring the Enigmatic Concept
-
Biography9 months ago
Chevy Chase Net Worth, Bio, Age, Height, Wife & Family